Cat Next Generation machinery has been going from strength to strength, setting the standard for productivity, accuracy and safety on site
It has been five years since the first Cat Next Generation machines were launched in Australia through Hastings Deering – bringing smarter ways of working to the construction industry.
Equipping machinery owners and operators with real time data and technology to support greater accuracy and safety on the worksite, the Next Gen range now covers excavators, wheel loaders and soil compactors – allowing operators to get more done in less time, save on fuel and reduce safety risks.
When Caterpillar released the Next Generation excavators, they changed the industry and what the industry expects from earthmoving equipment and onboard technology
Hastings Deering HEX product specialist George Brown says.
"It’s not just technology – everything from the powertrain, pumps and transmission through to the design of the operator cabin basically changed what operators could do going forward".
Brown says the underlying technology within the Next Gen machines support businesses in two ways. At the operational level the fleet manager or owner is supplied with information around machine performance, maintenance and material moved; whereas at the operator level it aids with achieving a greater level of accuracy and reduction of waste.
“Efficiency comes through the elimination of human error, as operators are working to a design,” Brown says.
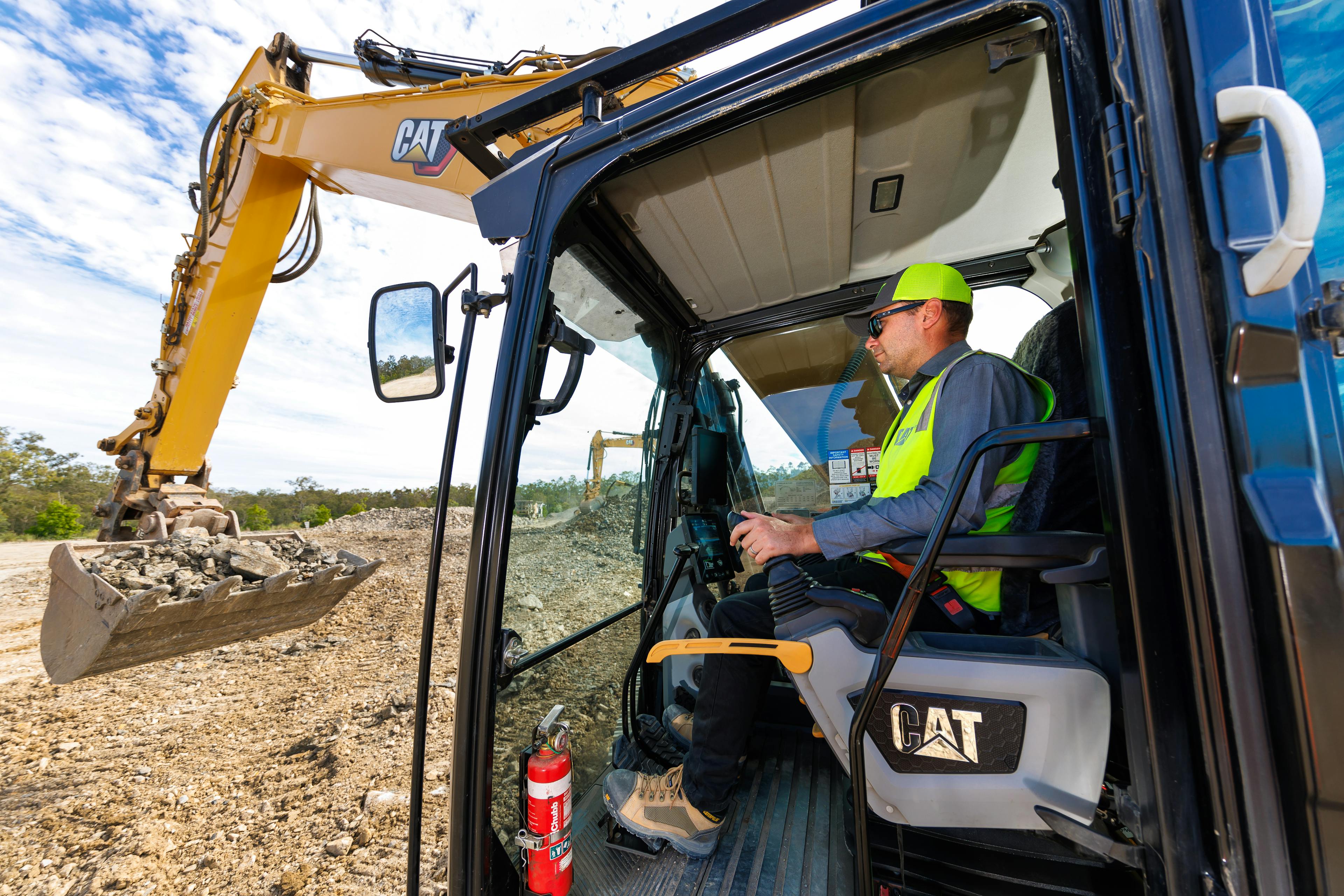
Operators can dig to design every time with Cat Next Generation machinery.
“What Caterpillar prides itself on is that, with their technology, the operator can operate to the design with assist features, which prevents them from over-digging.
“The Next Generation excavators have grade control, payload management systems and e-fencing. And then there is Lift Assist for when a job site requires a suspended load. When it comes to our Next Generation wheel loaders, they’ve also got Cat payload systems and job site applications to tailor the machine performance to that specific job at hand.
“With our paving equipment they also operate to design. It might be as simple as the integrated compaction measurement system [Machine Drive Power] to eliminate unnecessary passes in both granular or soil material, or there’s also compaction mapping where the operator can map the pass counts to make sure they’ve reached the desired compaction.”
With greater accuracy on site comes greater productivity and reduced fuel and maintenance costs. Alongside improved fuel efficiency, Caterpillar has also focused on improving maintenance costs – such as through extending the life of filters, extended service intervals and simpler maintenance tasks, for example.
Hastings Deering has also put the power of integrated machine technology and connectivity into the hands of its customers with its HD360 digital platform to further improve productivity.
“We’ve connected people with their investment [Cat machinery] and created a fast, easy-to-use tool to manage their business. It also acts as a gateway to a multitude of Cat apps, such as VisionLink, with single sign on to make access even simpler and easier,” Brown says.
With the VisionLink app, the machinery owner can see idle times of machinery, identify assets that are not performing profitably, manage downtime and keep track of any maintenance or repair alerts.
Safety
As well as a suite of technology to support improved productivity on site, equally as important is keeping the operator and others working around the machine safe.
To reduce safety risks, Cat Next Generation machinery allows for E-Fencing to prevent a machine from entering hazardous areas – for example, setting a height limit to prevent an excavator from contacting overhead power lines.
Lift Assist actively measures the payload being lifted and instructs the operator on what their allowable movements are, keeping operation within a safe working range.
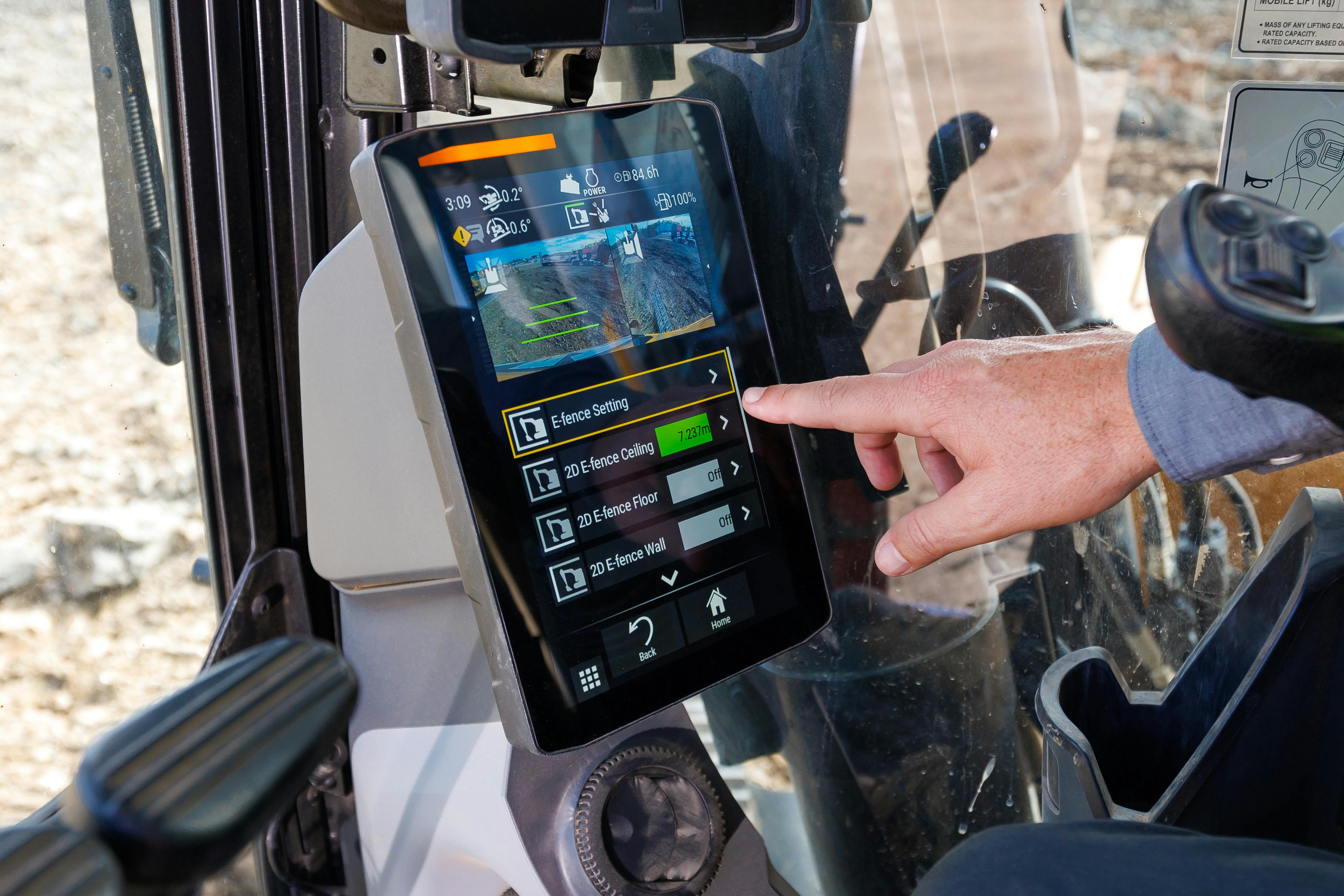
With E-Fencing, machine movement can be restricted to a set area.
The payload management system for wheel loaders and excavators means that they can accurately load haul trucks, ensuring that they are within the allowable weight limit for road transport.
Finally, a 360-degree camera system provides a complete view around the machine to remove blind spots.
“The market has absolutely loved what these machines can do,” Brown says.
“Once the operator sits in the seat and enjoys the operator features – not only technology-wise, but also the comfort and the room in the cabins – they tell you they really cannot go back to how they’ve done things traditionally. They only see the possibilities that open up to them in the future.
"The Cat next generation equipment is the intelligent choice for heavy duty projects", he adds.
On the ground
One Hastings Deering customer who has been using a variety of Cat Next Generation machinery since it was first released is Digwright owner and managing director Andrew Wright.
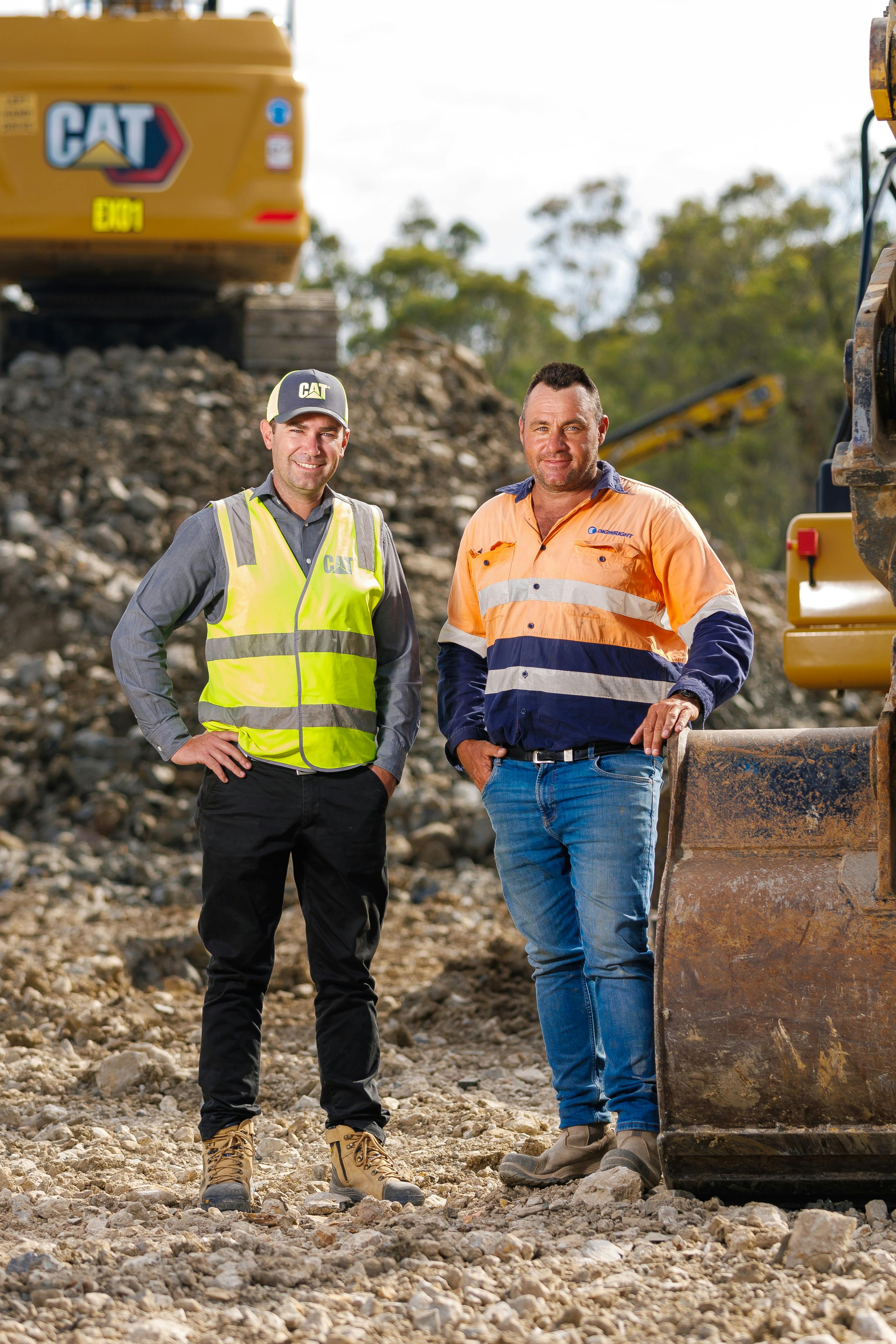
Hastings Deering sales representative Steve Rykiert (left) with Digwright owner and managing director Andrew Wright.
A civil/mining contractor and plant hire supplier servicing South East Queensland, Digwright has a variety of Cat Next Generation excavators, including two 349s, two 340s, a 330, a 323 and a 326, as well as a Cat Next Generation D6 dozer.
The machinery is being run on a number of sites, including a mine rehabilitation project near Ipswich and crushing and screening material with their client Earthtrak for the Coomera Connector project.
At the mine site, several of the excavators are undertaking bulk loading and earthworks, redistributing and compacting old mine stockpiles while the D6 dozer was used for pushing out material and final trimming work.
On Digwright’s crushing and screening project, surplus spoil from development work is being fed into a crusher by Cat Next Generation excavators, to be converted into fill for road building.
On both projects, Wright says Cat’s Next Generation machinery has been invaluable for maintaining productivity and accuracy.
“We’ve got GPS on all of the machines – Cat Grade Control – and this allows us to dig to level straight away and improve our productivity as operators can see where they are on the job,” he says.
“It allows us to plan ahead for work. We can trim to tolerance with no overcutting or rework.”
The ability to track payload information has also been a vital tool for his team.
“With the Chain of Responsibility laws, being able to measure our payload keeps us in check with loading trucks,” Wright says.
“It means we can ensure we’re loading to the correct weights. We can also track our productivity while crushing, by weighing what we put through the crusher to make sure we are on target. Through VisionLink we can download real time payload information so we can track the machine through the day, see where it’s up to and try and make production targets.”
When asked how easy it has been for his operators to understand and utilise the various capabilities of the Cat Next Generation machinery, Wright says it’s been a simple and straightforward process to get them up to speed.
“It doesn’t take long to show somebody the basics and then it can be as powerful as you want it to be,” Wright says.
“The guys like that they can customise the operator settings to suit them or the work they’re doing.
“You can just use the system for basic information, or you can drill right down into the data for times, weights, asset location, material types, the status of individual trucks that are being loaded. It allows us to do multiple tasks at the same time and something we use every day to track our progress, especially with the crushing and screening.”
When asked how the safety systems benefit him and his staff, Wright says not only do they reduce risks on site, but also make his business stand out from others by having this advanced technology in place.
“Having the ability to set height limiters and other e-fencing, especially around rail corridors and road works under power lines, provides that added factor that ticks a big safety box for us and our clients, and anyone that’s working around the machine,” he says.
With other brands you may have to fit aftermarket cameras, object detection or limiters, whereas it’s an all-in-one platform on the Cat Next Gen machinery.
“We have excellent backup support from Hastings Deering as well, and having the VisionLink and the HD360 digital platform behind it makes it all makes it a great experience.”
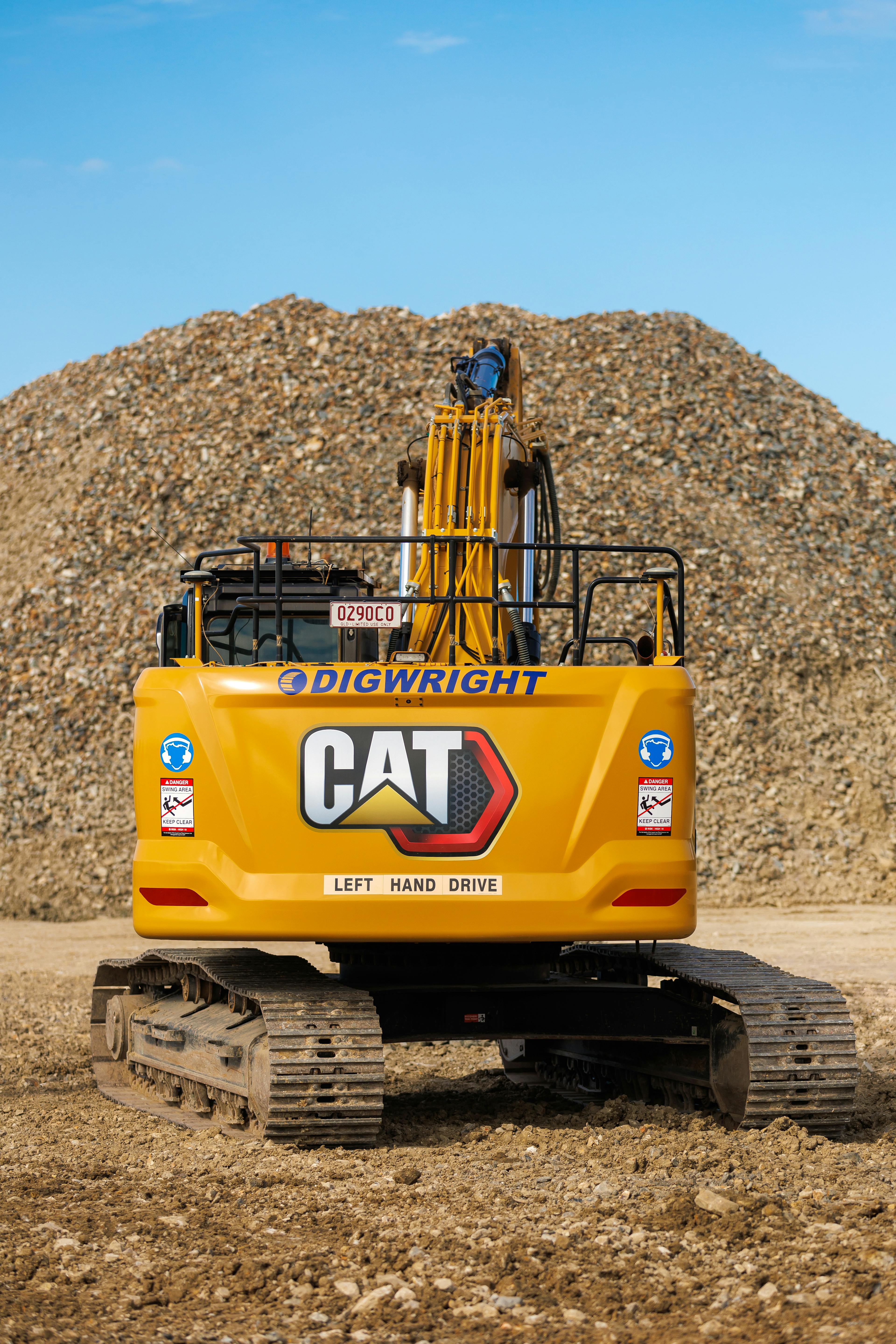
Cat Next Gen technology helps fleet owners achieve greater efficiency on site.
For more information on Cat Next Generation Machines click here
Credit: Article written by Trade Earthmovers